Удельная теплоемкость,
кал/г-град, при температуре, °С:
0
…………………………………………… 0,06430
500
………………………………………… 0,068875
700
………………………………………… 0,07086
900
………………………………………… 0,07316
1100
………………………………………. 0,07564
1300
………………………………………. 0,07852
1500
………………………………………. 0,08118
1600
………………………………………. 0,08267
Коэффициент
линейного расширения,
α*10-6,
1/град., в интервале температур, °С:
20 — 100 ………………………………….… 6,09
20 — 200 …………………………………… 6,58
20 — 300 ………………………………….… 6,97
20 — 400 ……………………………………. 7,33
20 — 500 ……………………………………. 7,55
20 — 600 ……………………………………. 7,69
20 — 700 ……………………………………. 7,59
20 — 800 …………………………………….. 7,59
Коэффициент сжимаемости при 30°С,
см2/кг ……………………….. 0,570*106
Удельное сопротивление
ρ*106,
ом см, при
температуре, °С:
0 ……………………………………………… 15,22
100 …………………………………………… 19,18
300 …………………………………………… 27,09
500 …………………………………………… 35,0
600 …………………………………………… 38,96
Температурный коэффициент электросопротивления при 20°С
… 3,95*10-3
Температура перехода в сверхпроводящее состояние, °С
………. -263,8
Работа выхода электронов,
эв …………………………………………. -4,01
Потенциал ионизации,
эв ……………………………………………….. 6,77
Электронная эмиссия,
а/см2, при температуре,
°С:
1327 …………………………………………. 2,19*10-5
1727 …………………………………………. 1,16*10-2
2127 …………………………………………. 0,800
2527 …………………………………………. 60,67
Положительная эмиссия,
эв …………………………………………….. 5,52
Коэффициент Ричардсона,
а/см2 ……………………………………….. 37
Коэффициент вторичной эмиссии ………………………………………. 1,18
Удельная магнитная восприимчивость при 18°С,
э.м.е …………….. 2,28•10-6
Магнитная проницаемость,
э.м.е, при температуре, °С:
20 ………………………………………………. 2,410 + 0,6*10-6
-196 ……………………………………………. 2,4 +
0,6*10-6
-253 ……………………………………………. 2,5 +
0,6*10-6
Излучаемая мощность,
в/см2,
при температуре, °С:
1327 …………………………………………….. 6,40
1727 …………………………………………….. 18,5
2127 …………………………………………….. 45,4
2527 …………………………………………….. 130,6
Коэффициент излучения при λ = 6650А, 20°С
……………………………. 0,37
Эффективное сечение поглощения тепловых нейтронов, барн/атом .1,1
Основная
масса полуфабрикатов и изделий из ниобия и его сплавов получается из плавленого
металла.
Плавка
осуществляется в электронно-лучевых или электро-дуговых печах при остаточном
давлении 10-4
- 10 5
мм рт. ст.
Способ плавки оказывает существенное влияние па
чистоту металла и его физико-химические и технологические свойства. Наличие
незначительных примесей (сотые доли процента) кислорода, азота, водорода и
углерода приводит к образованию оксидов, нитридов, карбидов и других сложных фаз, которые,
выделяясь по границам и внутри зерен, резко снижают пластичность и повышают
прочность и твердость ниобия. В табл.
1 приведены механические свойства ниобия.
Табл. 1.
Механические свойства ниобия различной чистоты
Способ
выплавки металла |
Содержание примесей внедрения, % |
Вид и состояние полуфабрикатов |
Механические свойства |
σb,
кГ/
мм2 |
σ0,2,
кГ/
мм2 |
δ,
% |
HB,
кГ/ мм2 |
Электроннолучевая плавка |
0,004 - С,
0,005
-
N2, 0,0015 - 02, 0,0008 - Н2 |
Лист
холоднокатаный (степень деформации 70%) н отожженный при 1000“ С 30
мин |
34,8 |
29,3 |
49 |
70 |
Электродуговая
плавка |
0,05 - С,
0,03
-
N2, 0,05 - 02, 0,002 - Н2
|
Лист холоднокатаный (степень деформации 90%) и отожженный при
1100“ С 1
ч |
45—50 |
35—40 |
25—30 |
100— 120 |
Прочность
ниобия можно значительно повысить (в 1,5—2 раза) путем холодной деформации. При
отжиге деформированного металла происходит снятие наклепа и его разупрочнение.
Изменение механических свойств показано на рис.
1.
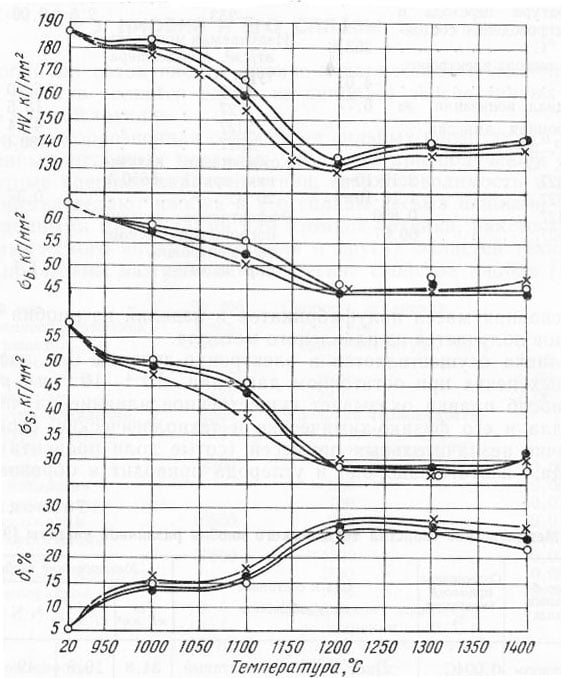
Рис.1.
Изменение механических свойств ниобия в зависимости от температура отжига: белый
кружок - выдержка 10 мин, черный кружок - выдержка 30 мин., крестик - выдержка
60 мин.
Полный отжиг
ниобия соответствует температуре 1200° С.
При
высокотемпературном отжиге (1450° С и выше) отмечаются интенсивный рост зерна
(собирательная рекристаллизация) и появление выделений по границам зерен.
Такие
изменения в структуре приводят к резкому снижению ударной вязкости ниобия. Так,
например, ниобий, отожженный при 1200° С, имеет
а„ = 37
кГ -м/см2,
после отжига при 1450° С
ан = 1,5
кГ-м/см2 . В отличие от вольфрама и молибдена ниобий при комнатной
температуре обладает высокой пластичностью и допускает общую деформацию до
80—90%. Порог хрупкости технического ниобия с содержанием 0,03% 02,
0,03%
N2,
0,05% С лежит при температуре
минус 180—200° С.
Увеличение
содержания примесей внедрения вызывает повышение температуры перехода ниобия из
пластичного в хрупкое состояние. Влияние
этих примесей на температуру пластично-хрупкого перехода показано на рис.
2.
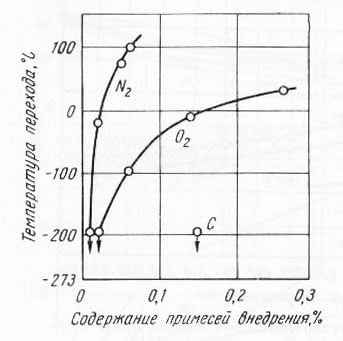
Рис. 2.
Влияние примесей внедрения на температуру пластично-хрупкого перехода ниобия
При нагреве
на воздухе с 200°С ниобий заметно окисляется. С повышением температуры
окисляемость сильно возрастает.
На рис.
3, по данным, показано изменение окисляемости
ниобия в зависимости от температуры и времени нагрева. Резкое повышение
окисляемости ниобия при 1000°С и выше связано не только с увеличением скорости
диффузии кислорода, но и с качественными изменениями, происходящими в структуре
окисной пленки. При температуре 1000—1100°С происходит переход
низкотемпературной модификации окисла
α-Nb2O5 в высокотемпературную
модификацию
β-Nb2O5,
сопровождающийся значительным
увеличением объема (в 2,7 раза), что приводит к возникновению внутренних
напряжений и локальным разрушениям пленки и ее отслоению. Последнее вызывает
резкое повышение окисляемости ниобия.
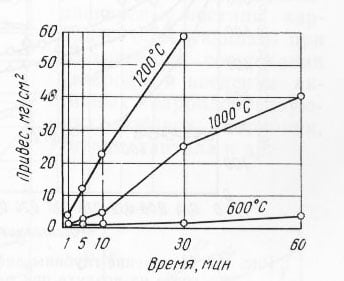
Рис. 3.
Окисляемость ниобия при различных температурах
При нагреве ниобия наряду с его окислением
происходят диффузия и растворение газов в металле. Предельная растворимость
кислорода в ниобии при 500°С составляет 0,25% (по массе), при 1915°С 0,72% (по
массе); азота при 300°С 0,005% (по массе), при 1500°С 0,07%.
При большом
содержании азота и кислорода образуются нитриды
(NbN,
Nb2N
и др.) и различные
окислы.
На рис.
4. показано изменение глубины диффузионного слоя в зависимости
от температуры нагрева. Образование газонасыщенного слоя приводит к резкому
повышению твердости и снижению пластичности ниобия. При нагреве тонкостенных изделий может проходить сквозная
диффузия, что приводит к полной порче металла. Учитывая сильную окисляемость
ниобия и его активное газопоглощение, нагрев проводится в вакууме (при
остаточном давлении 10-5—10-6
мм рт. ст.) или в среде очищенных нейтральных газов (аргона,
гелия). При работе в атмосферных условиях при высоких температурах для деталей и
изделий из ииобия требуются специальные жаростойкие покрытия. В качестве
защитных покрытий применяют
MoSi2,
Сг — Al —Si
и др.
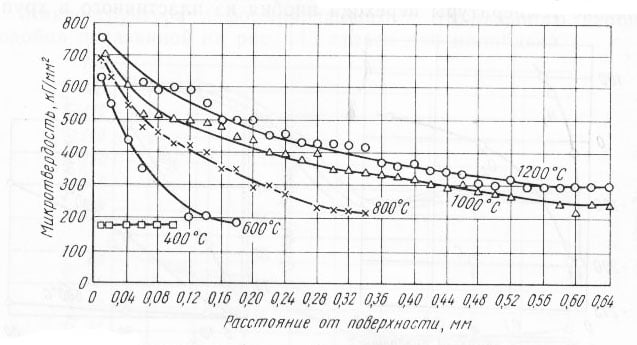
Рис. 4.
Изменение глубины диффузионного слоя ниобия при одночасовом нагреве на воздухе
при различных температурах
Значительно
более лучшими свойствами, чем ниобий, обладают сплавы на его основе. Влияние
различных легирующих добавок на механические свойства ниобия при комнатной и
повышенных температурах показано на рис. 5 и 6.
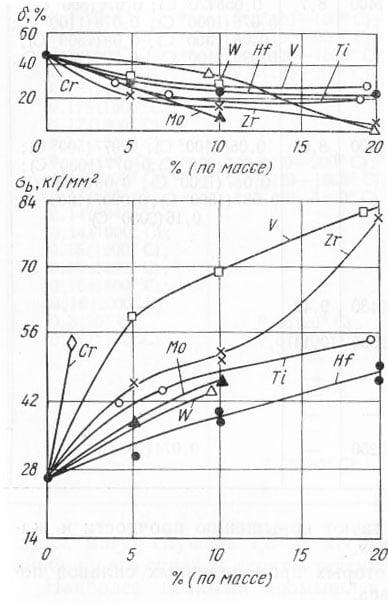
Рис. 5.
Влияние легирующих компонентов на механические свойства ниобия при комнатных
температурах
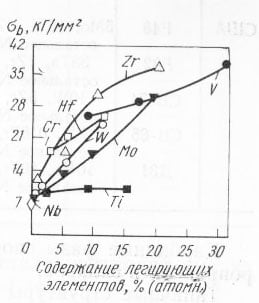
Рис. 6.
Влияние легирующих добавок на механические свойства ниобия при температуре 1095°С
Как видно из
приведенных данных, наиболее эффективное упрочнение сплавов при высоких
температурах достигается от введения вольфрама, молибдена, циркония, титана,
гафния, ванадия. Они в основном и применяются для легирования ниобиевых сплавов.
Состав и
физические свойства важнейших промышленных сплавов ниобия приведены в табл. 2.
Изменение механических свойств некоторых сплавов в зависимости от температуры
показано в табл. 3.
Табл. 2.
Состав и физические свойства промышленных ниобиевых сплавов
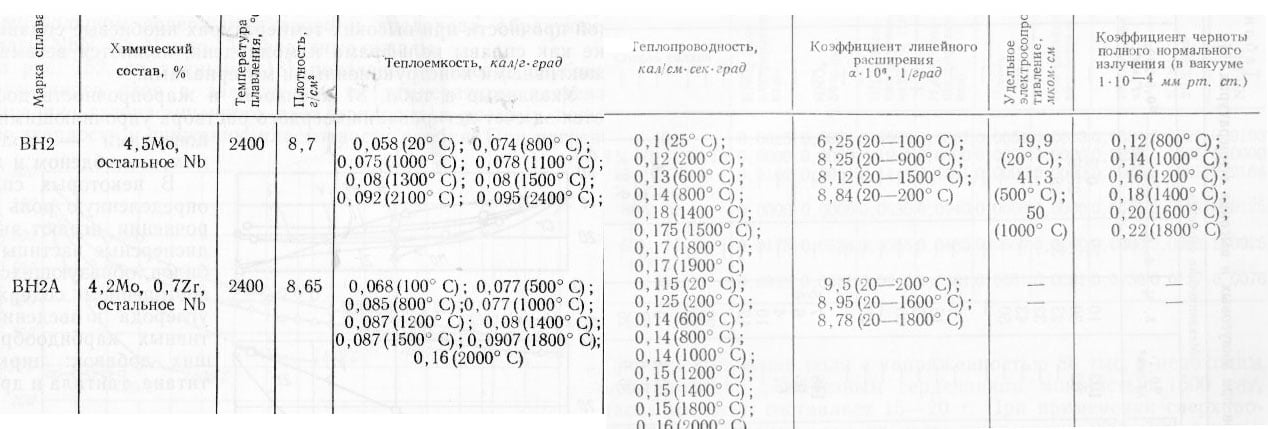
Таким
образом, по показателям кратковременной и длительной прочности при высоких
температурах ниобиевые сплавы, так же как сплавы вольфрама и молибдена, являются
весьма перспективными конструкционными материалами.
Указанные в
табл. 3 прочность и жаропрочность достигаются за счет легирования твердого
раствора упрочняющими компонентами — вольфрамом, молибденом и др.
В некоторых сплавах определенную роль в
упрочнении играют высокодисперсные частицы карбидов, образующихся при
повышенном содержании углерода и введении активных карбидообразующих добавок:
циркония, титана, тантала и др.
Табл. 3.
Механические свойства промышленных ниобиевых сплавов при минусовых и высоких
температурах
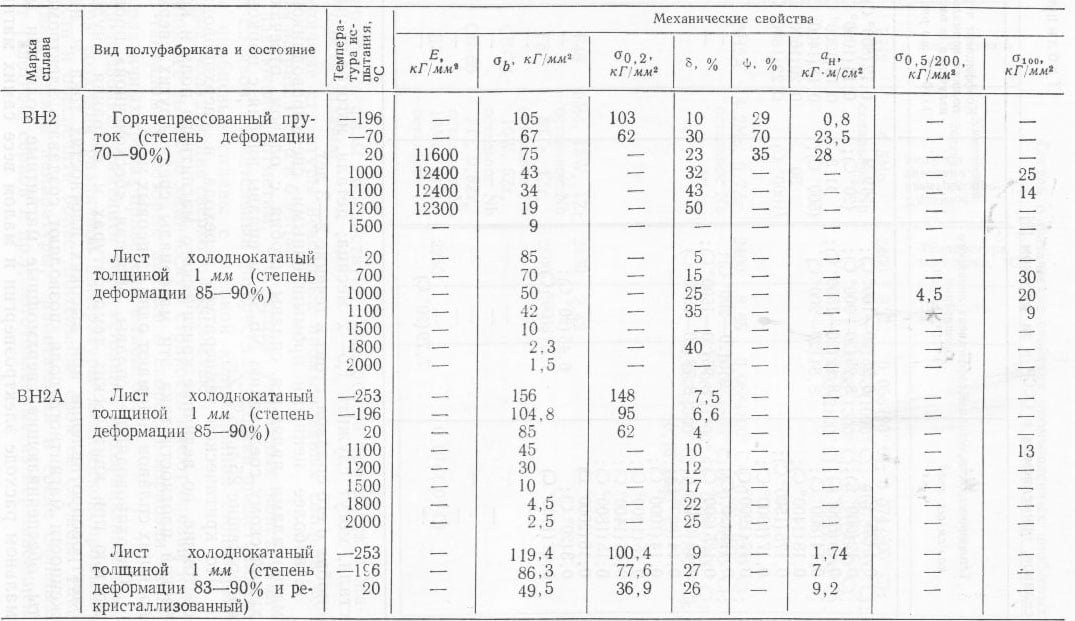
По своей
структуре все ниобиевые сплавы можно разделить на две группы: сплавы типа
твердых растворов и сплавы с гетерофазной структурой.
К 1-й группе
относятся сплавы ВН2, ВН2Л, СВ-65,
Fe-82
и др., имеющие однофазную структуру сложнолегированного
твердого раствора.
К 2-й группе
относятся сплавы
F48,
СВ-74 и др. структуры которых
состоит из зерен твердого раствора и включений высокодисперсных частиц карбида
циркония.
Карбидные
фазы способствуют повышению прочности и жаропрочности сплавов.
В заключение
отметим, что, кроме указанных конструкционных сплавов, значительный интерес для
техники представляют также ниобиевые сплавы с высокой коррозионной стойкостью и
сплавы, обладающие сверхпроводимостью.
Наиболее
высокую химическую стойкость имеют сплавы ниобия с танталом. Некоторые данные о
скорости коррозии сплавов в различных средах приведены в табл. 4.
Табл. 4.
Скорость коррозии сплавов ниобий - тантал, мм/год
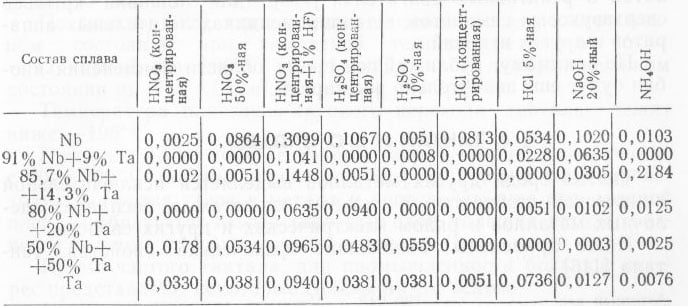
Они позволяют
заменить дорогостоящий и дефицитный тантал при создании различной аппаратуры
химической промышленности и обеспечить более длительный срок ее службы. Так,
например, детали аппаратуры, работающей в среде сильных кислот (азотной, серной
и др.), изготовленные из нержавеющей стали, могут служить 1,5—2 месяца; детали,
изготовленные из ниобия и его сплавов, стоят в течение 2—3 лет.
Наиболее
ценными промышленными сверхпроводниковыми материалами являются сплавы ниобия с
оловом, отвечающие химическому соединению
Nb3Sn,
и
сплавы ниобия с цирконием, содержащие 25 и 75%
Zr.
По
критической температуре перехода в сверхпроводящее состояние, по величине
критического магнитного поля и критической плотности тока эти материалы среди
других сверхпроводящих сплавов занимают одно из первых мест.
Сверхпроводящие сплавы, обладая «бесконечной» проводимостью при критических
температурах и сохраняя «нулевое» электросопротивление при высоких плотностях
тока и напряженности магнитного поля, позволяют создавать электромагниты,
обеспечивающие сверхмощные магнитные поля при минимальном расходе электроэнергии
и малом весе самих магнитов. Так, для получения поля с напряженностью 88 тыс.
э необходим электромагнит с железным сердечником мощностью
1500
кет,
масса которого составляет 15—20 т. При
применении сверхпроводящих соленоидов вес их составляет всего 200—300
г, при этом потребляемая мощность снижается на 4—5 порядков.
В настоящее
время ниобий и его сплавы применяют в различных областях науки и техники.
В
значительных количествах ниобий и его сплавы используют в электровакуумной
технике и радиоэлектронике для изготовления сухих электролитических
конденсаторов, деталей электро- и радиоламп, катодов косвенного нагрева, а также
в производстве выпрямителей.
В химической
промышленности ниобий и его сплавы применяют в качестве конструкционных
материалов для изготовления змеевиков, дистилляторов, трубопроводов, клапанов,
корпусов и других деталей химической аппаратуры для производства соляной и
азотной кислот, перекиси водорода и др.
Некоторые
ниобиевые сплавы применяют в ракетной технике для изготовления сопловых насадков
взамен охлаждаемых титановых, в теплообменниках космических аппаратов, для
изготовления деталей ионных и плазменных двигателей, для обшивки спускающихся на
землю ракет и капсул и др.
Широкое
применение ниобиевые сплавы получили в реакторах для плакировки
тепловыделяющихся элементов, для трубопроводов, труб охлаждения и деталей
насосов. Ниобиевые сверхпроводящие сплавы применяют в сверхмощных атомных
ускорителях, для изготовления обмоток магнитов для отражателей горячей плазмы,
квантовых генераторов и других ядерно- энергетических установок. Известно также
применение ниобиевых сплавов в авиационной технике для изготовления турбинных
неохлаждаемых лопаток в реактивных двигателях, для обшивки крыльев
сверхзвуковых самолетов, в теплообменниках летательных аппаратов и других издели.