Прокатка металла
Прокаткой называют процесс обжатия заготовки между вращающимися валками
с
целью придания ей требуемых формы и размеров. Процесс
прокатки
осуществляют следующим образом (рис. 1).
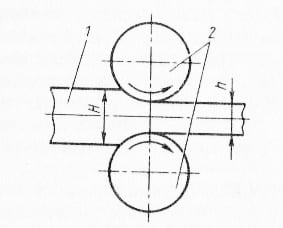
Рис. 1. Схема прокатки
Полоса 1 толщиной Н силами трения, возникающими между ее поверхностью и
поверхностью вращающихся валков 2, втягивается в щель между ними.
Высота щели меньше начальной высоты прокатываемой полосы, поэтому после
пластического обжатия конечный размер полосы будет меньшим
h.
Разность между начальным и конечным размерами полосы называют
абсолютным обжатием.
Заготовку могут пропускать между валками несколько раз, добиваясь
необходимого абсолютного обжатия. Эту величину ограничивают в силу
нескольких причин. При очень малом обжатии время прокатки
увеличивается, металл остывает и для его прокатки требуются большие
усилия. При слишком большом обжатии в заготовке могут образоваться
трещины. Вот почему для каждой заготовки рассчитывают скорость вращения
валков, расстояние между ними, учитывая при этом прочностные
характеристики материала.
При
прокатке уменьшение толщины полосы вызывает рост ее ширины. В
металлургии этот процесс называют
уширением.
Его учитывают при расчете размеров заготовки. Например, если уширение
будет значительно больше расчетного, то образуются излишки металла по
ширине, он будет выдавливаться в зазор между валками, образуя излишний
элемент - заусенцы, который необходимо удалить. Большинство металлов и
сплавов недостаточно пластичны в холодном состоянии, и для прокатки их
предварительно нагревают до определенной температуры.
Кратко рассмотрим основные конструктивные узлы оборудования для
прокатного производства.
Валки для прокатки
- рабочий инструмент для прокатки металлов. Каждый валок представляет
собой цилиндр, отлитый из прочного чугуна или стали. Для прокатки полос,
листов и пластин валки изготавливают гладкими. Для получения фасонного и
сортового проката применяют калиброванные валки, в которых по окружности
выточены канавки той или иной формы. Их называют ручьями. При наложении
одного валка на другой образуются просветы определенного профиля.
Например, необходимо прокаткой изготовить двутавровую балку (рис. 2б).
Ее прокатывают поэтапно. Сначала прокатывают балку
1
с помощью роликов
2
и
3
(рис. 2а).
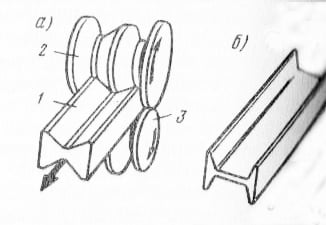
Рис. 2. Схема прокатки двутавровой балки
Затем в несколько этапов получают окончательную форму прокатываемого
профиля. Примеры таких профилей приведены на рис. 3. Изменяя форму
валков и расстояние между ними, можно получить различный сортамент
прокатных профилей.
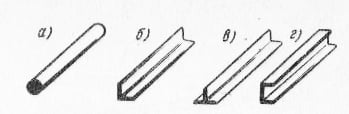
Рис. 3. Виды прокатки: а - пруток;
б - уголок; в - тавр;
г - двутавр
С
помощью прокатки получают специальные профили. Рассмотрим, Например,
прокатку гильзы, из которой затем получают бесшовную трубу (рис. 4).
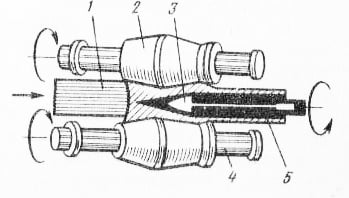
Рис. 4. Изготовление трубопровода прокаткой
Здесь
пруток
1
подают в пространство между вращающимися в одну сторону валками
2 к 4,
установленными друг относительно друга под небольшим углом (от 8 до
24°). Пруток в этом
случае
нагревают. Между валками, на пути движущегося прутка, устанавливают
конусную оправку
3,
обычно называемую
дорном.
Он и образует внутреннюю полость цилиндрической формы. Получается
пустотелый с толстыми стенками профиль - гильза 5. Этот процесс называют
прошивкой.
Гильза после прошивки имеет толстую стенку, (доходящую до 20%
от диаметра трубы. Кроме того, на ее поверхности (остаются следы валков
и дорна в виде винтовых линий. После этого с помощью обработки на других
прокатных станах получают тонкостенную трубу заданного размера с гладкой
поверхностью.
Прокатный стан
- машина для обработки металлов давлением между вращающимися валками. В
некоторых производствах прокатный стан представляет собой систему машин,
куда входят, кроме собственно прокатного стана, машины для резки
проката, правки, сматывания в бухты или рулоны готовой продукции
(например, тонких листов), транспортирования прокатанного материала.
Основной частью прокатного стана является
рабочая клеть,
(рис.
5), состоящая из станины
1,
валков
2
и шпинделей
3.
Валки
приводятся во вращение шпинделями, соединенными через редукторы и муфты
с электродвигателем. В прокатном стане могут быть одна
или
несколько клетей.
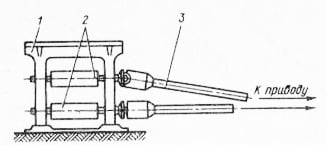
Рис. 5. Прокатный стан
По
назначению станы разделяют на два основных типа: станы
дли
прокатки полуфабриката, являющегося исходной заготовкой
для
получения сортового проката, и для выпуска готового проката.
К
первому типу относят
обжимные станы
-
блюминги
и
слябинги.
Их
используют для прокатки слитков весом до 25 т. На блюмингах получают
блюмы
- заготовки квадратного сечения (200x200
и 350x310)
и слябы -
заготовки прямоугольного сечения (до 1600 мм ширины и ли 300 мм
толщины).
Ко второму типу относят следующие станы: рельсобалочные -
для
получения сортового проката, проволочные (для проволоки диаметром 5 - 10
мм), листовые и трубные, а также станы для получении специальных видов
проката.
По конструктивному выполнению различают станы по числу и расположению
валков в рабочей клети. Схемы расположения ваков изображены на рис. 6.
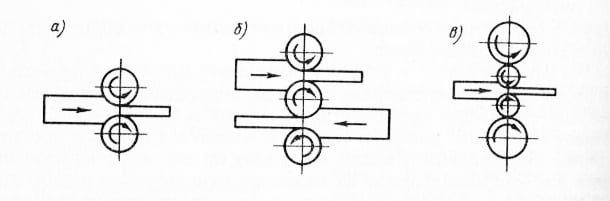
Рис. 6. Схемы станов: а - дуостаны;
б - триостаны; в - квартостаны
Станы с
двумя валками называют
дуо.
Они имеют два горизонтальных валка. Станы, где в клети расположены три
валка, называют
триостаны.
В клети трио прокатку производят в обе стороны. Как видно из рисунка, в
одну сторону идет прокатка между верхним и средним валками, а в другую -
между средним и нижним валками.
Клети,
имеющие четыре валка - два рабочих меньшего диаметра и два опорных
валка, называют
квартостаны.
Квартостаны широко применяют для горячей прокатки толстых и тонких
листов, а также для холодной прокатки тонких листов и лент. В
квартостанах получают большую точность листа по толщине из-за отсутствия
прогиба валков, поскольку усилие деформации валков малого диаметра
воспринимается валками большего диаметра. Имеются также многовалковые
станы, которые применяют для холодной прокатки тончайшей ленты.
.
|