Оловосодержащее сырье и способы его переработки
Основным
минералом олова является касситерит, представляющий собой оксид олова (SnО2).
Меньшее
практическое значение имеет другой минерал - смешанный сульфид олова, меди и
железа - станнин (Cu2FeSnS4).
Содержание олова в рудах обычно составляет 0,1-3%. Руды оловянных месторождений
можно подразделить на россыпные и коренные.
Россыпи обычно
значительно легче обогащаются гравитационными методами, чем руды коренных
месторождений, они не требуют применения дорогостоящих процессов дробления,
измельчения.
Доводка черновых концентратов легко осуществляется магнитными,
электрическими и другими методами.
В России около
95% олова извлекается из коренных, обычно очень сложных и труднообогатимых,
тонковкрапленных руд, требующих развитых схем обогащения, применения флотации.
В соответствии
с вещественным составом руды, свойствами входящих в нее ценных минералов и
минералов пустой породы, а также с применяемым для обогащения руд процессом,
коренные оловянные руды можно классифицировать на следующие основные
технологические группы: руды, обогащаемые гравитационными методами; руды,
обогащаемые комбинированными гравитационно-флотационными методами, руды,
обогащаемые комбинированными флотационно-гравитационными методами.
Возможность
применения гравитационных методов обогащения обусловлена тем, что минералы олова
тяжелее большинства минералов вмещающей породы. Сульфиды железа, меди, свинца и
некоторых других примесей могут быть отделены от касситерита флотацией (иногда
этот процесс совмещается с гравитацией и тогда носит название флотогравитации).
Для удаления магнитных минералов применяют магнитную сепарацию, а минералы,
резко отличающиеся от касситерита по электропроводности, удаляют с помощью
электростатической сепарации. Содержание олова в концентратах,
предназначенных для плавки, составляет обычно 40-70%.
Технологическая схема металлургической переработки оловянных концентратов
включает в себя следующие основные переделы: удаление из концентратов вредных
примесей обжигом, выщелачиванием или последовательным осуществлением обеих
названных операций; восстановительную плавку концентратов на черновое олово;
рафинирование (очистку) чернового олова с получением марочного (т.е.
соответствующего по составу стандарту) металла (рис. 1).
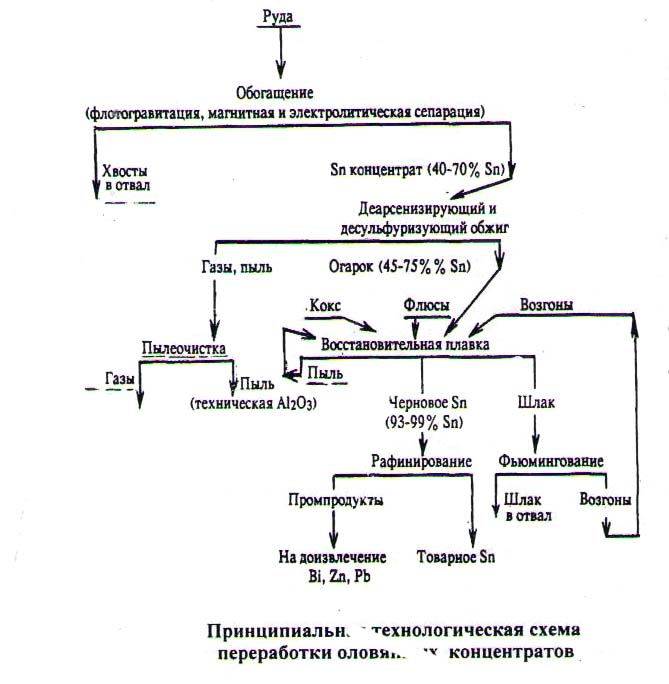
Кроме
перечисленных операций в технологическую схему входят дополнительные операции по
переработке полупродуктов производства: шлаков, пылей и др. Цель обжига
концентратов - удаление из них примесей мышьяка и серы, осложняющих последующие
операции выщелачивания (если оно проводится после обжига), плавки и
рафинирования. Мышьяк в оловянных концентратах содержится главным образом в виде
минерала арсенопирита (FeAsS),
а сера,
кроме того, - в виде пирита или пирротина.
Серу и мышьяк
удаляют при обжиге за счет термической диссоциации (разложения под действием
высоких температур) и окисления. В результате мышьяк и сера возгоняются в
элементарной форме или в виде оксидов, содержащееся в указанных выше минералах
железо переходит в
Fe203
или
Fe304.
На
отечественных предприятиях обжиг оловянных концентратов осуществляют в
многоподовых печах, либо в печах кипящего слоя (КС), за рубежом - в основном в
трубчатых вращающихся печах.
Оловянные
концентраты обжигают в многоподовых печах при 650-850°С. Повышение температуры
обжига способствует полноте отгонки мышьяка и серы, но может привести к спеканию
лежащего на подах материала. Показатели работы этих печей: удельная
производительность 0,15-0,3 т/(м2.сут),
расход угля или кокса 30-130 кг на 1 т обжигаемого концентрата.
Степень
деарсенизации (удаления мышьяка) - до 70-80%, а десульфуризации (удаления серы)
- до 80-95%, конечное содержание каждой из примесей в обожженном
концентрате не более 0,3-1%. Выход обожженного концентрата (огарка) 80-95% от
массы исходного концентрата. Потери олова при обжиге 0,2-1,3%.
При обжиге
оловянных концентратов в трубчатых вращающихся печах обжигаемый материал
постоянно пересыпается, поэтому температуру обжига можно поднять до 1000°С и
выше без опасения образования спеков. Благодаря этому удается повысить полноту
отгонки мышьяка и серы, а в ряде случаев наряду с этими примесями удалить также
менее летучие свинец и висмут.
Технология
обжига оловянных концентратов в печах кипящего слоя основана на интенсивном
взаимодействии обжигаемого материала с перемещающим его воздухом. Обжиг в печи
КС производят при температуре 780-820°С, создаваемой за счет выделения тепла по
экзотермической реакции окисления серы или (в случае малого содержания последней
в концентрате) за счет сгорания угля, добавляемого в количестве до 60-100 кг на
1 т концентрата.
Производительность печи КС в расчете на 1 м2 площади пода значительно
выше, чем производительность многоподовой печи, и составляет до 25 т/(м2.сут).
Степень деарсенизации достигает 75-90%, степень десульфуризации 85-98%.
Газы,
выделяющиеся при обжиге оловянных концентратов, очищают по следующей схеме: в
первую стадию улавливают оловосодержащую пыль в горячем электрофильтре при 300°С
(мышьяк при этой температуре еще не конденсируется), во вторую стадию -
мышьяковые возгоны в мокром электрофильтре при температуре не выше 80-120°С (это
необходимо для обеспечения полной конденсации мышьяка). Уловленные по такой
схеме оловянные возгоны содержат не более 0,3-1%
As,
в то
время как мышьяковые возгоны содержат 71-73%As
и
являются, по существу, техническим триоксидом мышьяка (As203).
Концентраты,
поступающие на плавку, обычно содержат, %: 45-75
Sn;
1-4
Fe;
до 0,1
Pb;
до 0,01
Bi;
0,2-0,5
As;
0.1-0.4
S;
0,4-2
W03;
до 25
Si02;
0,1-4
CaO;
0,2-3
Аl203.
Олово восстанавливается из касситерита оксидом углерода уже при 500-600°С по
схеме:
SnО2
→
SnO
→
Sn,
т.е.
сначала до низшего оксида, а затем до металла.
В
отечественной практике восстановительную плавку оловянных концентратов
осуществляют только в электротермических печах, а за рубежом - также в
отражательных, барабанных вращающихся и других печах.
Электропечи
для плавки оловянных концентратов имеют мощность 350-3000 кВА при площади пода
2-11 м2. Площадь пода отражательных печей 24-46 м2.
Восстановительную плавку оловянных концентратов в электропечах и отражательных
печах ведут при 1150-1350°С.
Удельная
производительность электропечей по концентрату составляет 3-7 т/(м2.сут);
удельный расход электроэнергии 800-1200 кВт.ч/т. Прямое извлечение олова в
черновой металл при восстановительной плавке составляет 90-95%; остальное
количество распределяется между оборотными пылями и шлаком, направляемым на
фьюмингование с целью доизвлечения из него олова.
Железистые
шлаки восстановительной плавки оловянных концентратов содержат, как правило, не
менее
5%
Sn.
При
фьюминговании степень отгонки олова - до 90-98%.
Получаемый в
результате восстановительной плавки оловянных концентратов и оборотных продуктов
(пылей, фьюминг-возгонов и др.) черновой металл содержит, %: 93-99Sn;
0,2-,5Fe;
0,2-2
As;
до 0,1
S;
до 3
Pb;
до 2 Си;
до 3,5
Sb;
до 0,4
Bi.
Черновой металл очищают огневым или электролитическим рафинированием до
следующего, например, состава, %: < 99,92
Sn;
0,10
As;
0,009
Fe;
0,01Cu;0,025
Pb;
0,01Bi;
0,015
Sb;
0,01
S;
0,002
Zn;
0,002
Al.
Огневое (реагентное)
рафинирование чернового олова применяют в отечественной и зарубежной практике.
Метод заключается в обработке расплавленного металла различными реагентами с
последовательным удалением примесей железа, мышьяка, меди, сурьмы, висмута и
свинца.
Железо до
содержания 0,1% удаляют обработкой чернового олова при 350-450°С элементарной
серой, переводящей железо в форму сульфида. Для облегчения снятия тяжелых
железистых съемов в расплав после обработки серой иногда вмешивают при 500-600°С
мелкий уголь. Всплывая он увлекает с собой соединения железа. Одновременно с
железом удаляется часть мышьяка и меди.
Удаление
мышьяка до содержания 0,01% достигается обработкой чернового олова при 500-
600°С алюминием, образующим с мышьяком тугоплавкие интерметаллические соединения.
После рафинирования от мышьяка в черновом олове остается до 0,05-0,1% алюминия.
Его удаляют хлористым аммонием при 300-320°С, используя реакцию 2Аl +
6NH4Cl
= 2АlСl3
+
6NH3
+ 3Н2.
Одновременно с
мышьяком при обработке алюминием удаляется железо до содержания не выше
0,02%,
а также частично медь и сурьма (указанные примеси, как и мышьяк, образуют с
алюминием интерметаллические соединения).
Медь до
содержания не выше 0,1% удаляют, как и железо, с помощью элементарной серы.
Температура расплава при этом составляет 220-350°С.
Удаление
сурьмы осуществляют аналогично удалению мышьяка при 550°С с помощью обработки
алюминием. Наряду с удалением сурьмы в этой операции олово окончательно
очищается от остатков железа, мышьяка и меди.
Удаление
висмута реагентным методом основано на образовании им интерметаллических
соединений с магнием и натрием. Эти реагенты вмешивают в расплав при
температурах соответственно 380-400 и 240-300°С. После снятия висмутовой пены
при 280-350°С удаляют с помощью хлористого аммония остаточные магний и натрий (аналогично
удалению остаточного алюминия). В этой операции вместе с висмутом удаляются
остатки сурьмы.
Удаление
свинца основано на реакции
Pb +
SnCl2
= PbCl2 +
Sn,
идущей
слева направо при температуре ниже 450°С. Возможно также прямое удаление свинца
из чернового олова обраооткой элементарным хлором при 250-270°С.
Реагентное
рафинирование олова проводят в чугунных или стальных котлах полусферической
формы рабочей емкостью (по олову) 5-45 т, обогреваемых электрическим или
природным газом.
Общая
продолжительность полного цикла реагентного рафинирования обычно 40-80 часов,
удельная производительность котлов по олову 2-6 т/сут на 1 м3 объема.
Прямое извлечение олова в марочный металл составляет 80-90%, остальное олово
переходит в съемы и возгоны.
Плавку
проводят в небольших электропечах (200-500 кВА) или отражательных печах при
1300-1400°С. Разовая загрузка съемов составляет 2-5 т, продолжительность плавки
3-6 часов, удельная производительность печей для переплавки съемов 5-10 т/(м2.сут)
Черновой
металл, полученный в результате переплавки съемов и возгонов рафинировочного
передела, обычно используют для производства сплавов (баббитов).Шлак после
насыщения оловом до содержания
20%
(через 2-8 плавок) направляют на восстановительную
плавку, заменяя его свежим.
Висмутовые
съемы (пену) подвергают специальной переработке с целью концентрирования
висмута. Хлористые (свинцовистые) съемы обрабатывают жидким цинком (25-35% от
массы съемов), цементирующим из них олово и свинец по реакции:
SnCl2
+
Zn =
Sn +
ZnCl2
и PbСl2
+
Zn
=
Pb +
ZnCl2.
Эту операцию
проводят при 400-480°С, продолжительность ее составляет 6-9ч. Полученный
оловянно-свинцовый сплав направляют на рафинирование, и цинковистые съемы - на
гидрометаллургическую переработку.
В
отечественной практике освоены физические методы рафинирования олова -
центробежный и вакуумный. При центробежном рафинировании жидкое олово
фильтруется через слой кокса под Бездействием центробежных сил.
Операцию
осуществлют при 310-400°С. В результате удается очистить черновое олово до
конечного содержания железа не более 0,1%, мышьяка - не более 0,1%. В фильтрат
извлекается 80-85%
Sn,
остальное количество переходит в съемы, содержащие 50-65%
Sn,
5- 20%
Fe,
5-25%
As
и
направляемые обычно на обжиг вместе с оловянными концентратами.
Вакуумное
рафинирование позволяет очистить олово от летучих примесей (свинца и висмута) в
результате обработки чернового олова при 1000-1300°С и остаточном давлении 13-
65 Па.
Операцию
проводят в индукционных или вакуумных электрических печах непрерывного действия
производительностью до 20-25 т/сут. В результате вакуумного рафинирования
содержание свинца в черновом олове может быть снижено с 1-3 до 0,03-0,22%, а
висмута - с 0,1-1,5 до 0,01-0,06%. Извлечение олова в рафинированный металл
составляет 99,8%. Первичный конденсат, выход которого составляет 4-6% от массы
олова, содержит,
%:
15-35
Sn;
40-60
Pb;
6-10
Bi;
до 1,5
Sb. Его
подвергают многократной вакуумной разгонке с целью доизвлечения олова и
концентрирования висмута. После четырех - пяти таких операций можно получить
товарный конденсат, содержащий, %, не более: 2-3
Sn;
65-92
Pb;
7-25
Bi;
до 3-4
Sb;
0,1-0,2
As,
и
направляемый на извлечение висмута.
|